Whispers of Graphite: Unraveling the Mystery of Ribbon Composition
There's a particular scent that hangs in the air when you're around a vintage typewriter: a blend of dry paper, lubricating oil, and a faint, almost metallic tang. That last element? It’s the ghost of the ribbon, a silent witness to countless letters, poems, and manifestos pressed onto yellowed pages. We often think of the typewriter itself as the star of the show – the mechanical marvel with its intricate levers and satisfying clacks. But the ribbon? The ribbon is the soul. It’s the vital thread that transforms intention into tangible form. Understanding what it’s *made* of is understanding a small piece of history, a whisper of graphite and ingenuity.
My own fascination with typewriter ribbons began, as so many things do, with a forgotten inheritance. My grandfather, a quiet man of letters and meticulous habits, left behind a collection of typewriters. Not gleaming, showroom-ready machines, but well-loved companions, bearing the marks of countless hours of dedicated use. Among them were spools of ribbons, some brittle and faded, others surprisingly intact. Handling those ribbons, feeling the delicate texture, I felt a connection to him, to the process of creation, and to a time when communication demanded a certain deliberate slowness.
The Early Days: Silk and Lampblack
The first typewriter ribbons weren’t precisely what we recognize today. Early machines, like the Sholes & Glidden, utilized inked fabric, often a loosely woven muslin. This wasn’t a ribbon in the modern sense; more like a saturated cloth that would leave a blotchy, often uneven, impression on the paper. Improvements came rapidly, however, driven by the burgeoning demand for clear, consistent typewritten documents. The evolution was inextricably linked to the development of the printing industry, drawing upon techniques and materials already established for ink production.
The core ingredient, of course, was carbon – specifically, finely ground lampblack. Lampblack is soot created by the incomplete combustion of oil, typically vegetable oil or coal oil. Its origins are ancient; artisans have used it for centuries to create black pigments for paints and dyes. The quality of the lampblack was crucial; coarser particles resulted in a grainy, less-defined print. The fineness of the pigment was largely dependent on the quality of the furnaces and the skill of the lamplighters – truly, a craft born of observation and experience. The subtle nuances in these pigments, and how they affect the final impression on paper, could almost be considered an art form in themselves – a complexity we further explore in articles dedicated to deciphering the secrets in ribbon color variations.
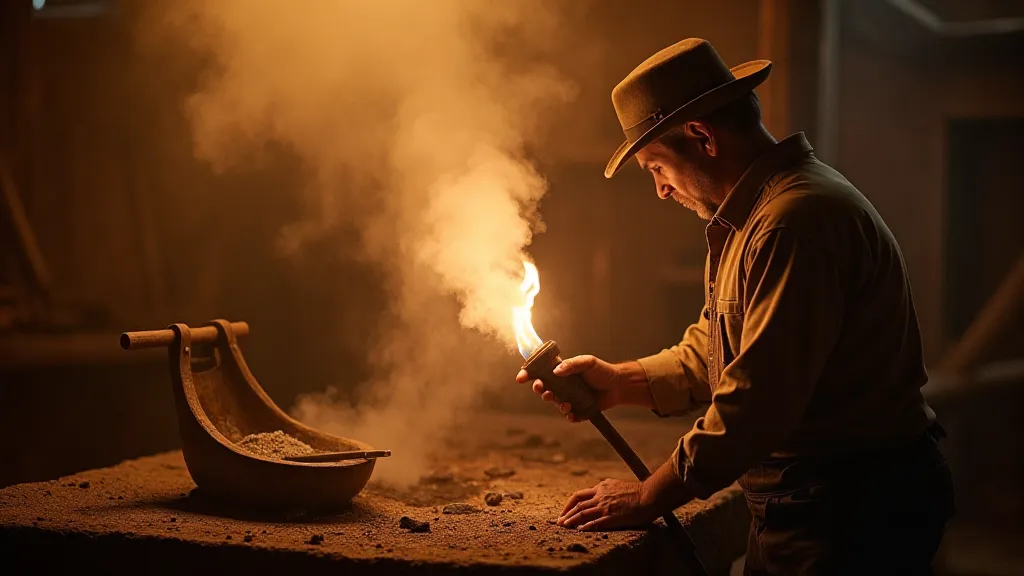
From Silk to Nylon: A Shifting Landscape of Materials
The carrier fabric initially used was silk. Silk offered a smooth surface and a degree of elasticity that allowed the ribbon to wrap neatly around the typewriter spools. But silk, while elegant, was expensive and prone to fraying. The search for a more durable and economical alternative led to the adoption of cotton, followed by linen. These natural fibers offered improved strength but still lacked the desired consistency and longevity.
The mid-20th century brought a revolution in materials science, and the typewriter ribbon was no exception. Nylon’s invention in 1935 marked a pivotal moment. Nylon’s strength, elasticity, and ability to be woven into fine, consistent strands made it ideal for typewriter ribbons. It virtually eliminated the issues of fraying and unevenness that plagued earlier ribbons. The process of applying the graphite mixture to the nylon carrier also evolved, moving from simple dipping and drying to more sophisticated coating techniques that ensured a more even distribution of the pigment.
Interestingly, the formula itself wasn’t always static. While graphite remained the primary coloring agent, manufacturers experimented with various binders to improve adhesion and print quality. Resins, shellac, and even glycerol were used, each imparting slightly different characteristics to the finished ribbon. Some ribbons were “waxed” to enhance their lubricity, making them smoother to feed through the typewriter. The marks left on the page, and the stories contained within them, are often layered and complex – a true palimpsest of letters, revealing a rich history with each impression.
Understanding the Degradation Process
The fragility of antique typewriter ribbons is a source of constant frustration for collectors and restorers. The familiar fading and brittleness aren’t simply a matter of age; they’re the result of complex chemical reactions accelerated by exposure to light, air, and moisture. The graphite particles, loosely bound within the ribbon's matrix, are susceptible to oxidation. This process weakens the binder and causes the pigment to disperse, leading to the characteristic fading and crumbling.
Light is a particularly damaging factor. Ultraviolet radiation breaks down the chemical bonds within the binder, accelerating the degradation process. Moisture, too, plays a crucial role. Water can penetrate the ribbon, promoting the oxidation of the graphite and dissolving the binder. The presence of acidic compounds, often found in old paper, can also contribute to the ribbon’s deterioration.
Sometimes, these failures can even lead to a unique form of beauty and creative inspiration. The unexpected marks and textures created by a degrading ribbon can be embraced as opportunities for reimagining ribbon failure as opportunity in creative writing, allowing for a new perspective on the writing process.
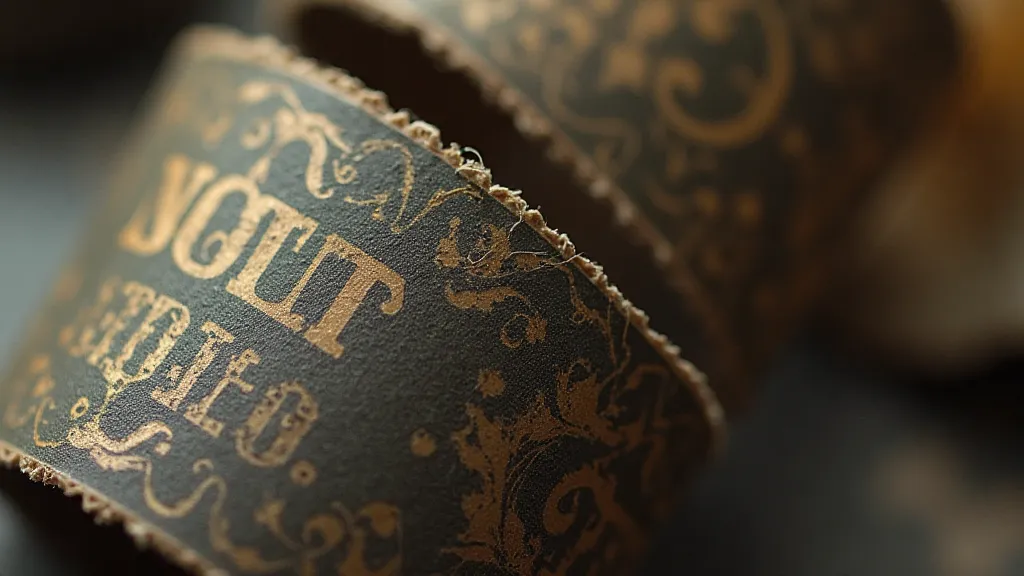
The Legacy of Craftsmanship
It's easy to take for granted the reliability of modern office supplies. We expect them to last, to perform consistently, and to be readily available. But the history of the typewriter ribbon is a testament to the ingenuity and craftsmanship of a bygone era. The creation of a high-quality ribbon involved a delicate balance of materials, techniques, and experience. From the lamplighter meticulously tending his furnace to the ribbon manufacturer carefully controlling the coating process, each step required skill and attention to detail.
The ribbons themselves are tangible links to the past, whispers of graphite and ingenuity that continue to inspire and intrigue. They remind us that even the most seemingly mundane objects can hold a rich and fascinating history. The subtle variations in color and texture across different ribbons offer a unique way of mapping subtle color shifts in antique ribbons, revealing geographical and temporal nuances in manufacturing processes.
Restoring or preserving these fragile remnants of the past isn’s just about keeping a piece of machinery running; it’s about honoring the individuals who crafted them and the countless stories they helped to tell. The faint, metallic tang in the air when you're around a vintage typewriter? That's not just a smell; it’s a legacy. The process of understanding and replicating these techniques requires a deep appreciation for the materials and the skill of the artisans. The knowledge required to accurately identify and categorize these ribbons is akin to a cartographer's skill, requiring meticulous observation and a deep understanding of the landscape. This dedication to detail is what allows us to truly appreciate the artistry and ingenuity of the past.
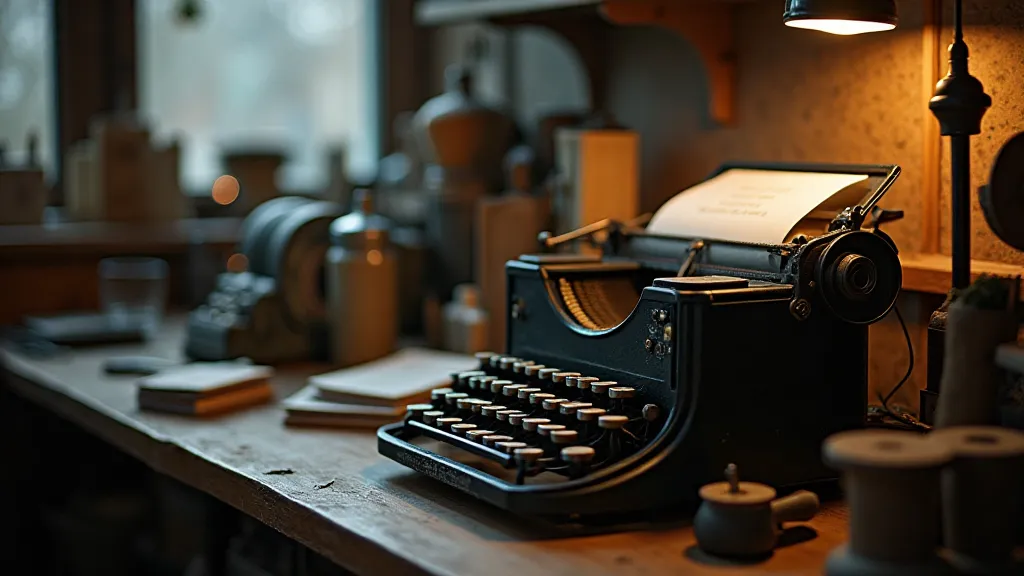
Beyond the chemical composition and material science, the story of the typewriter ribbon is interwoven with the social and economic forces that shaped the era. It represents a time when communication was a deliberate act, requiring care and precision. It speaks to a slower pace of life, where craftsmanship and attention to detail were valued. The ribbon serves as a reminder of the enduring power of human ingenuity, and the importance of preserving the tangible links to our past. Furthermore, continued research into these materials may unlock new applications in various fields, from art and design to engineering and medicine. The legacy of the typewriter ribbon is far from over, it continues to inspire and innovate in ways we are only beginning to understand.